We look after every step of the production process in our region for two reasons: to guarantee the highest quality fabrics and to respond in the fastest and most flexible way to the requests of clients.
Our belief is that Lanificio Zignone should oversee every step in the process here in the valleys of Biella, a region that for centuries has dedicated itself to excellence in textiles. Here, where the knowledge of wool is a shared knowledge, our group of workers is committed to every phase of the process – from the selection of raw materials to advanced finishing techniques. Those who select Zignone from among the many suppliers do so because our wool mill stands for precision and speed. Our trusted clients know that having direct control of the manufacturing process, as well as the most advanced machines, increases our ability to provide the best service and react to market needs.
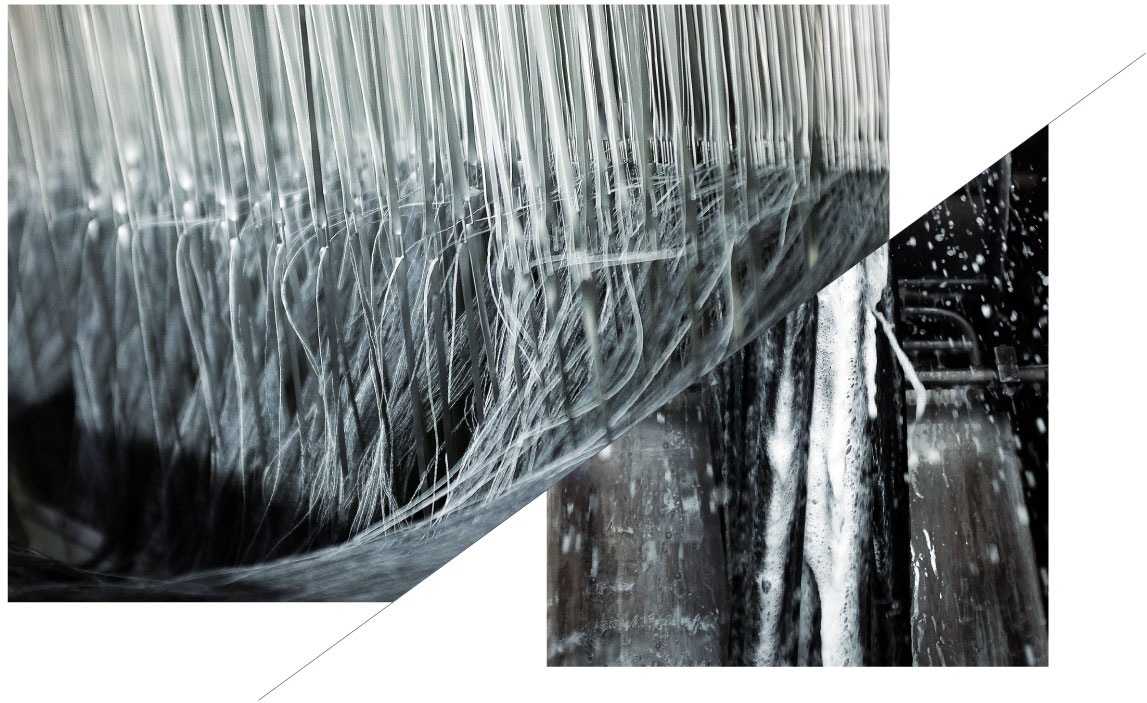
A tradition of top performance
Managing the entire supply chain to ensure competitive Made in Italy production
Advanced research into fabrics
On-going advances in wearability and a talent for innovation.
Elegance alone is no longer enough. The fashion industry looks for fabrics with more functional performance backed up by measurable performance data.
The wool mill has always combined aesthetic research with a great desire to improve the physical properties of its fabrics, starting with elasticity and the creation of innovative treatments for garments’ wearability that is in sync with people’s dynamic lifestyles. Zignone holds the patent for the world’s first family of machine-washable pure wool fabrics, known under the name ECO-WASH. The ability to embroider details directly on fabric bolts is another area in which the wool factory has made a name for itself in recent years.
Lastly, the collections from the most recent seasons include special processes to improve their functionality.
The Noblest Fibre
Zignone chooses the finest wool for its exceptional properties.
Due to its characteristics, wool is still the most popular fibre in clothing. It gives breathability to garments, allowing the exchange of air. Its thermoregulation properties keep the body warm in winter and cool in summer. It absorbs moisture then releases it in the air and is less susceptible to mould. Lastly, it is recyclable, reusable and biodegradable. Zignone selects its own wool from merino sheep in Australia and New Zealand, countries of wool excellence where the fineness of the fibres makes it possible to obtain softer and lighter fabrics. Managers personally inspect the farms to ensure the traceability of raw materials and the condition of the flocks.
The wool mill is a partner of the Cashmere and Camel Hair Manufacturers Institute, which works to verify and defend noble fibres (cashmere, mohair, alpaca) and fine or superfine wool (through the Superfine Wool Council).
Pure wool fabrics
The value of fabrics obtained exclusively from virgin wool.
To identify pure virgin wool fabrics the “Super” label is used together with a number that is proportional to the fineness of the raw material used. Super S fabrics adhere to the values shown in the following table.
“Super S” Number | Maximum number of the average diameterof the wool fibre |
“Super S” Number | Maximum number of the average diameterof the wool fibre |
---|---|---|---|
SUPER 80s |
19.75 µm |
SUPER 170s |
15.25 µm |
SUPER 90s |
19.25 µm |
SUPER 180s |
14.75 µm |
SUPER 100s |
18.75 µm |
SUPER 190s |
14.25 µm |
SUPER 110s |
18.25 µm |
SUPER 200s |
13.75 µm |
SUPER 120s |
17.75 µm |
SUPER 210s |
13.25 µm |
SUPER 130s |
17.25 µm |
SUPER 220s |
12.75 µm |
SUPER 140s |
16.75 µm |
SUPER 230s |
12.25 µm |
SUPER 150s |
16.25 µm |
SUPER 240s |
11.75 µm |
SUPER 160s |
15.75 µm |
SUPER 250s |
11.25 µm |
The analytical method to determine the average diameter of the fiber is specified in the regulation that defines the Code of Practice (Code of Conduct) of the IWTO.
Micron: conveys the fineness of the wool. The average diameter of the wool fibers is measured in microns. Lanificio Zignone uses wool ranging from 15 microns to 19 microns.
First-rate shearing
The search for quality starts with the selection of fleeces.
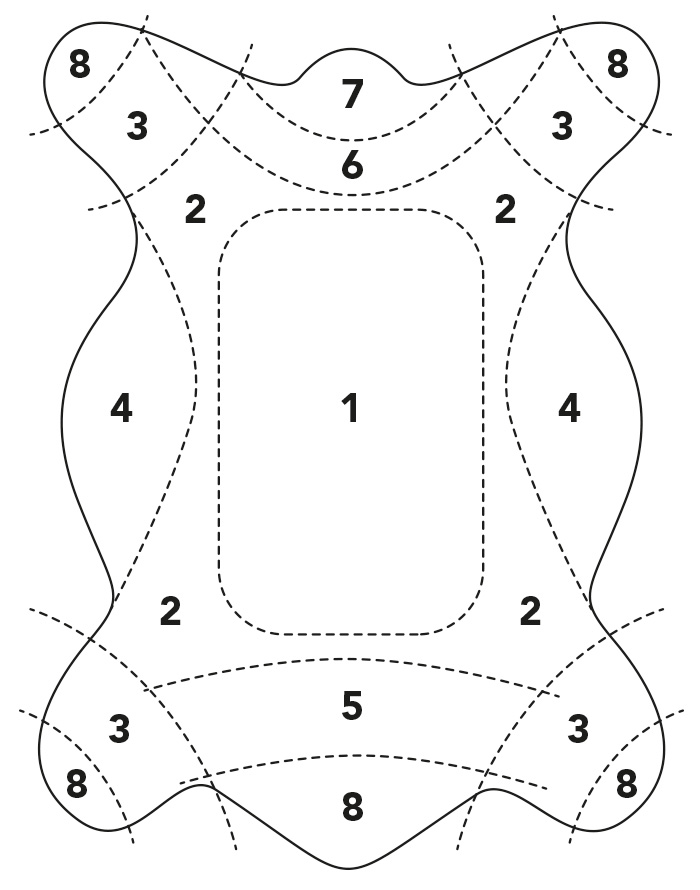
1 - FLEECES
Lanificio Zignone fabrics are produced using fleece, the back part of the animal, the best part because the fibres are long and clean. In some of flannels in the winter collections, skirting is also used.2 - BROKEN
A part which is manually removed from the fleece that has just been sheared - it is slightly shorter than fleece, however still nice and clean. It is the second nicer part of the fleece.
-
3 - PIECES
Shorter and less refined cuts that fall off and are removed from the fleece, extended along the border after shearing.
-
4 - BELLIES
Wool sheared from the animal’s belly that is flattened and very dirty with organic matter, since the sheep lies down on the ground to rest.
-
5 - NECKS
Wool sheared from the neck that is flattened and shorter.
-
6 - BACKS
Wool sheared from the hind, darker in colour and dirtier as this is where the sheep sits.
-
7 - STAINS
Parts that are very dirty, including black animal hair, usually of a yellowish colour as these are close to the genitals and get stained with urine.
-
8 - CRUTCHING
It is a mix of wool from the muzzle and the legs and is very short. It is usually used in the ‘Open’ and it is usually never combed because it its too short.
-
LOCKS
These are the shavings from the skirting, that is the very short fibres that fall onto the ground while shearing: when the sheared wool is taken and placed on a table to be selected. These are used in the ‘Open’ blends.
-
SHAKERS
Even these are very short fires that are used in mixed blends.
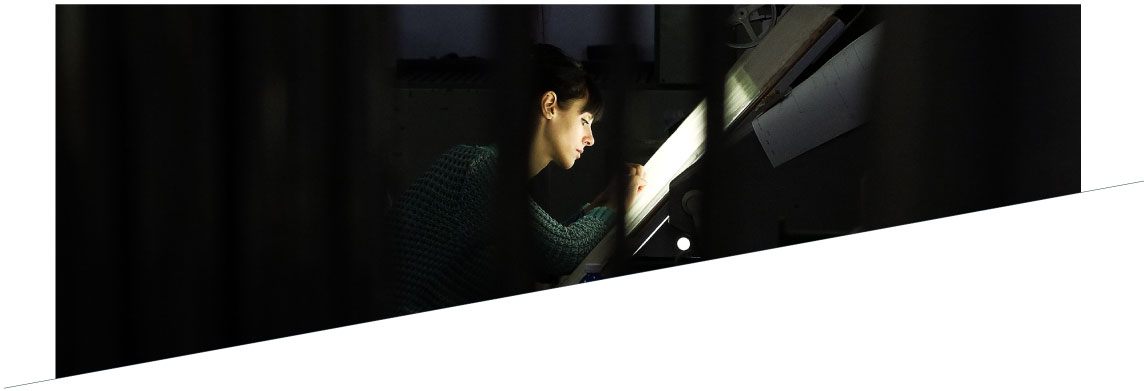
Oversight of the entire supply chain
Textile culture at work, from tops to the making of yarn.
Once in Italy, wool undergoes a transformation by way of small, complex operations that call for specialised skills. As a result, the natural raw material gives life to products of rare refinement, the result of the highest textile culture.
The wool mill entrusts the combing to a series of partner firms: the fibres are washed to avoid impurities and combed in order to create the “tops,” the soft wool ribbons intended for local dyers or sent directly to Zignone’s spinning mills. The Spaider factory is the main one: here, spinning takes place at fast speeds with the latest machinery for prepping and roving. In these processes the wool fibres are aligned, eliminating irregularities, increasingly thinning their dimensions and finally preparing the ribbon to be spun. Everything operates around an automated warehouse.
The “roving” is obtained from the finishers and then becomes for all intents and purposes yarn. Steamed, the yarn passes to the winding, where it undergoes ringing that makes it more resistant and gives different qualities depending on the method. The yarn on bobbins can be used as is and inserted as a weft thread during weaving. Or it can be twisted on itself or with other threads in the twisting phase to be then inserted as a warp. Lastly, the crimping and shrinkage phases, managed in a completely automated manner, precede the weaving.
Weaving and finishing
Fully focused on manufacturing elegance.
Weaving is the moment of enchantment and technical precision when a fabric comes to life. The warp and weft are intertwined with each other to give rise to the weaves – the union of horizontal and vertical threads – that vary according to the desired design.
Zignone handles all production inside its own facility. For weaving, the wool mill uses the latest generation looms, which rely on air flow to insert the weft threads instead of the traditional mechanical movements. Specialised workers then take care of quality control, eliminating residual impurities and perfecting the fabrics by hand via a process of darning and pre-finishing. In the case of fabrics still to be dyed, the fabrics proceed to the automated machines in the dyeing department. It is the moment of finishing, when the raw fabric finally obtains its distinctive qualities to the eye and touch – the appearance and the “hand” – according to the end use. Finishing is the most important phase of the entire production process, where precision is the priority to achieve the pleasure and comfort we are looking for in a piece of clothing. By managing all the treatments in-house, it allows Zignone to guarantee the highest standards even in the most advanced finishings.